The evolution of microstructural features and defects caused by high cycle fatigue loading has the potential to affect post-fatigue behavior and as such cause failure. To answer whether a component still meets design criteria after accumulating fatigue during service, we must understand that microstructural evolution. Our research group has performed a comprehensive series of fatigue, interrupted fatigue, and post-fatigue measurements on the 7075-T6 aluminum, alpha-Iron, and 403 stainless steel alloys to assess both quasi-static and dynamic mechanical properties after cyclic loading. The dislocation structures evolved from vein networks in region A below, into persistent slip bands (B) and finally formed dislocation cells (C).
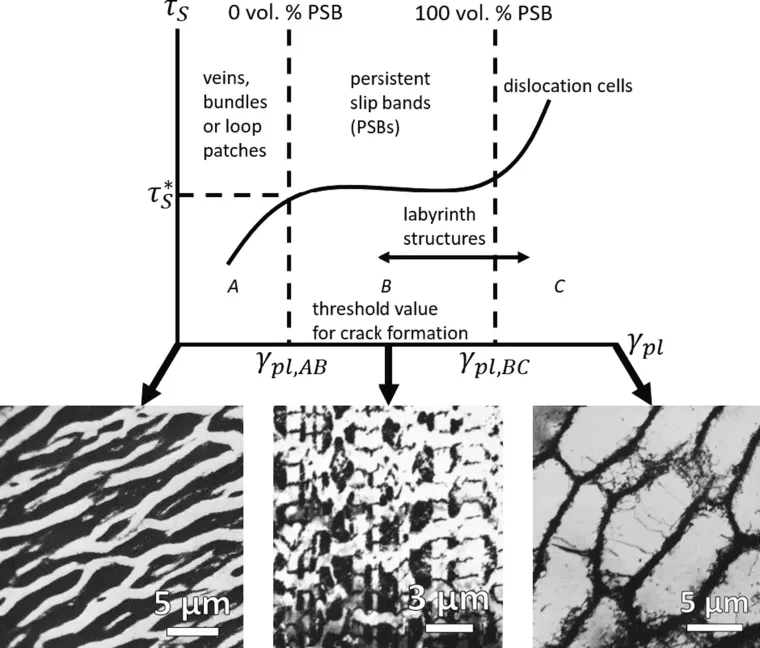
We found that the post-fatigue mechanical response of 7075-T6 aluminum was dependent on fatigue mean stress and subsequent loading strain rate, where tensile mean stress was required to produce any meaningful change (~7% loss) in resultant mechanical properties. It was also noted that the alloy's fatigue life may be extended by decreasing the size of iron inclusions and the number of inclusion cracks near the surface, though neither subsurface inclusion cracking nor dynamic loading affected the post-fatigue strength.
On another hand, we found decreases in the quasi-static yield stress and ultimate tensile stress between 31% and 94% of the fatigue life in alpha-Iron are due to increases in the average fatigue induced void size, total percentage of voids, and grouping of voids along the loading axis. Steady decreases in the yield stress were noticed and linked to the continually changing void sizes, whereas a sharp decline in the ultimate tensile stress was related to the increase of void volume and grouping of voids along the same axis.
News!
Our group is now equipped with an Instron 68TM-5 uniaxisal loading frame, an Instron 8801 uniaxisal loading frame, and an Instron 8852 multiaxisal loading frame, all of which can be utilized in conjunction with a short induction furnace.
These systems are capable of implementing unique loading profiles such as:
- Uniaxial monotonic and cyclic loading from room temperature to 1500°C
- Multiaxial tension-torsion room temperature to 1500°C
- Multiaxial fatigue: cyclic torsion and cyclic tension/compression at the same time from room temperature to 1500°C
- Several user-design loading profiles:
- constant torsion alongside different modes of fatigue, e.g., compression-compression, tension-tension, and tension-compression;
- cyclic torsion alongside with constant uniaxial tension or compression loading from room temperature to 1500°C.
This project sponsored by:
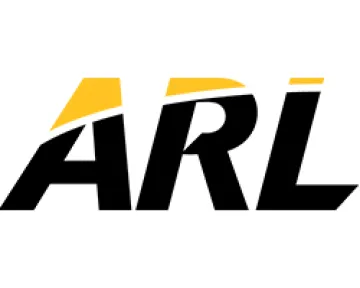
Relevant Papers